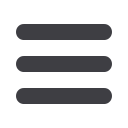
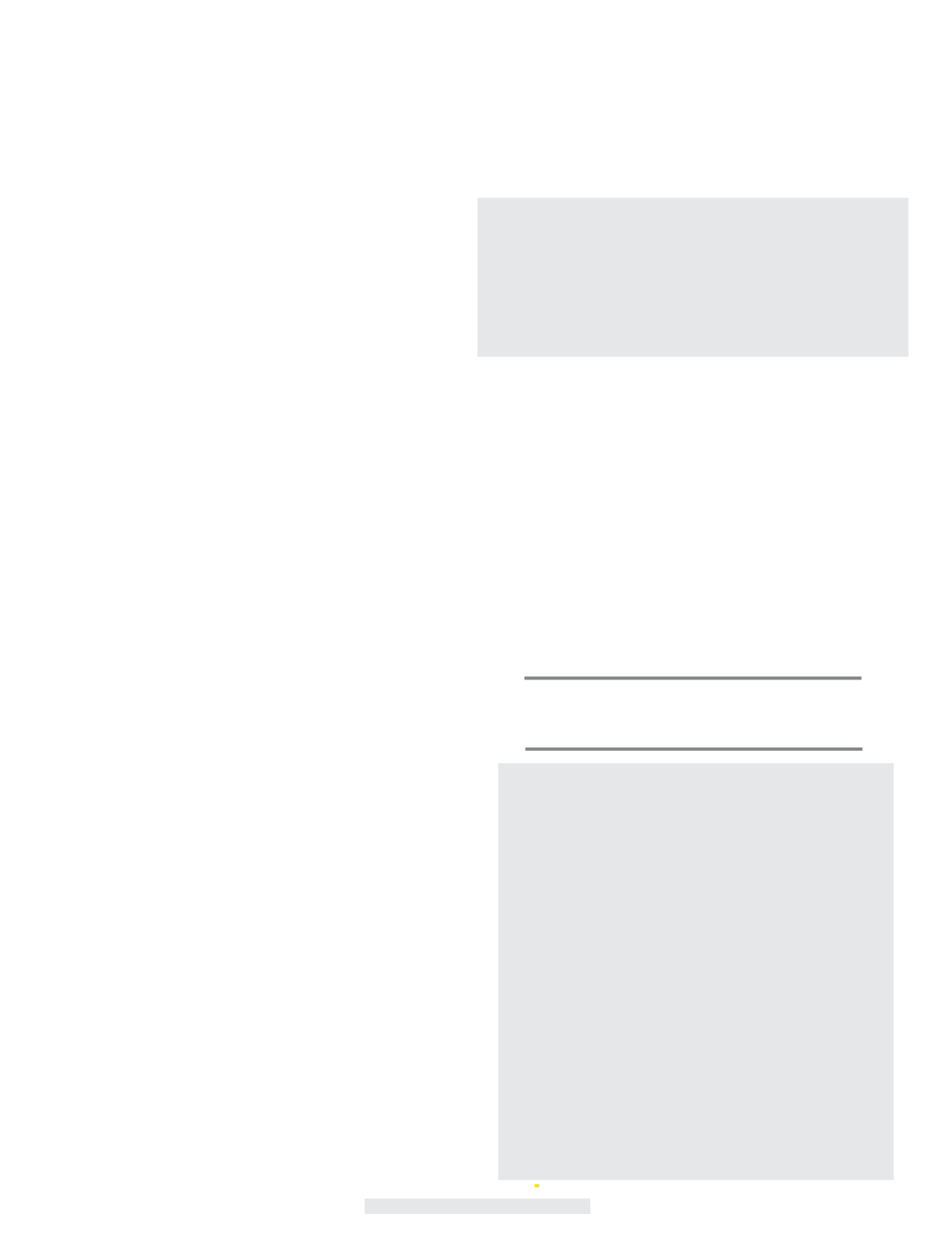
Holiday 2018
68
Disponible en línea en español.
“Did you know ?… “
A boat is built from the outside in? To carry out a repair the procedure is
done in reverse of how it was constructed. To appreciate a successful repair it’s
helpful to understand how the gelcoat & fiberglass shell is made.
Boats today are made using mostly three molds. A deck mold (top), hull mold
(bottom) and a pan mold; interior liner, cabin or cockpit furniture.
The first thing applied in the mold is sealer glaze A.K.A. parting material.
Gelcoat is then sprayed to a more or less uniform thickness against the
polished surface of sealer glaze. Gelcoat should be between 15-20 mils thick.
Inconsistencies in production often occur; I have seen gelcoat so thin you can
see through it and as thick as ¼”. Sometimes molds are dirty and the gelcoat
finish has defects and air pockets. If there are multiple gelcoat colors they are
also sprayed in reverse of what they appear on the finished product. Different
color layers of gelcoat are shown in the Doral repair image. The gelcoat
is then followed by one or two layers of chop strand fiberglass mat mixed
together with a resin binder. Chop strand fiberglass mat is the best for ease of
molding than other fiberglass material. No longer commonly used in today’s
production boat building due to environmental hazards the chop strand
fiberglass mat was applied with a chopper gun; a tool that chops continuous
strands of fiberglass into predetermined lengths and fires them into the mold
along with a fine spray of resin. The chop is coated with resin on the way to the
mold. Following is more on boat construction.
“Fiberglass GRP” Glass-Reinforced Plastic - Typically used for production
boats because of its ability to reuse a female mold as the foundation for the
shape of the boat. The resulting structure is strong in tension but often needs
to be either laid up with many heavy layers of resin-saturated fiberglass or
reinforced with wood or foam in order to provide stiffness. GRP hulls are
largely free of corrosion though not normally fireproof. These can be solid
fiberglass or of the sandwich (cored) type, in which a core of balsa, foam or
similar material is applied after the outer layer of fiberglass is laid to the mold,
but before the inner skin is laid. This is similar to the next type, composite,
but is not usually classified as composite, since the core material in this
case does not provide much additional strength. It does, however, increase
stiffness, which means that less resin and fiberglass cloth can be used in order
to save weight. Most fiberglass boats are currently made in an open mold,
with fiberglass and resin applied by hand (hand-lay-up method). Some are
now constructed by vacuum infusion where the fibers are laid out and resin is
pulled into the mold by atmospheric pressure. This can produce stronger parts
with more glass and less resin, but takes special materials and more technical
knowledge. Older fiberglass boats before 1990 were often not constructed
in controlled temperature buildings leading to the widespread problem
of fiberglass pox, where seawater seeped through small holes and caused
delaminating. The name comes from the multitude of surface pits in the outer
gelcoat layer which resembles small pox. Sometimes the problem was caused
by atmospheric moisture being trapped in the layup during construction in
humid weather.” Source- Wikipedia
In doing a repair we don’t have the beauty of the mold and care is taken
in every step to recreate the original shape and finish. Body lines and curves
in the boat are all done by hand and take a keen eye. What makes our job
interesting is that every repair is unique; holes, scratches, delaminating
fiberglass, impact fractures, cracks, air voids, boat pox, holes drilled in the
wrong place and production defects done by the manufacturer, improper plug
type repairs, failed or poorly done previous repairs, tree limbs crashing on
the deck crushing gunwales and windshields, fractured transoms, rotted floors
and stringers, weak winter storage roofs and temporary storage buildings
crashing on boats due to heavy snow loads, one boat that came to our shop
slid on its hull down I87 after it fell off its trailer. It came to a stop lying on its
side in the far left lane. The hull skidded so far that it wore through the gelcoat and
fiberglass on the port stern corner to the point of being able to see inside the boat.
Yes, it was repaired successfully after weeks of reconstruction.
Much thought goes into implementing a plan before our repairs are started and
being familiar with the construction of a boat insures that the repair is proper and
effectively done.
Take care of your vessel and it should give you years of happy boating!
Dr Gel
“Should my four year old boat have blisters on it already? The hull is
just covered with them; hundreds of them. The entire boat would need
to be stripped. I cleaned the boat at the end of each season with On-Off.
I contacted the dealer I purchased the boat from telling him about the
problem and he said I should have put bottom paint on it. The hull has a
Lifetime Warranty but the Gelcoat only a year! ” P.G.
I am not surprised that you have blisters on the hull of your four year old
boat. I have seen them on new boats. I just repaired a one year old hull with
numerous blisters and applied epoxy barrier coat on it. Luckily for the owner the
manufacturer paid for the blister repair. The manufacturer will pay for all future
blister problems as long as the hull has epoxy barrier on it.
Although rare, your boat manufacture may have this type of warranty.
Epoxy Barrier coat is cheap insurance when you consider the expense of doing
necessary osmotic blister repairs. The best time to apply barrier is when the boat is
new before blisters develop. Any age boat, especially those left in the water should
be protected!
Cleaning with On-Off or any acid wash will strip the algae and micro organisms
and will also strip the gelcoat protecting wax and sealer glaze. The porous
gelcoat is now more susceptible to water permeation and thus creates the perfect
environment for osmotic blisters to develop.
It is ok to use acid cleaners but it is essential to reseal the gelcoat with sealer
glaze and wax.
Have any questions? Email me at
boatrepair@aol.comWe would like to wish everyone a Happy, Healthy
and Prosperous New Year!
Merry Christmas
Happy Holidays to All!
Thank you for taking the time
to read “Ask Dr Gel”
I hope my articles have been
helpful and will continue to be!
To read more articles
2007-Present during the long
winter nights go to
www.boatingonthehudson.
com/past-issues